The quality of a wiring harness can significantly impact functionality and longevity in electrical systems. As a specialized wire harness manufacturer with comprehensive testing equipment and an excellent reputation, we adhere to strict quality control protocols. These six steps provide the framework to ensure that every wire harness we produce meets the highest industry standards.
- Material Inspection:
Quality begins with raw materials. Before production, all materials(including wires, connectors and jacketing)are thoroughly inspected to ensure defects-free and meet all required specifications. This proactive approach prevents potential problems that could later affect the performance of the harness.
2. Design verification:
Each harness must be carefully designed to meet the customer’s specific needs. During the validation process, engineers review the design to ensure accuracy and functionality. This includes verifying wire gauge sizes, connector types, and wire routing to optimize the efficiency of the final product.
3. Process standardization:
To ensure consistency, each assembly process step is standardized and documented in detail. This includes clear instructions for cutting, stripping, crimping, and assembling wire harnesses. Standardizing these procedures minimizes the risk of human error and ensures that each harness is identical to the last.
4. Automated and manual testing:
Our facility has state-of-the-art test equipment that performs automated tests on each harness. To ensure electrical safety, these tests may include continuity checks, insulation resistance measurements, and voltage withstand tests. In addition to automated tests, our skilled technicians perform manual inspections to identify and resolve any issues the machine may have missed.
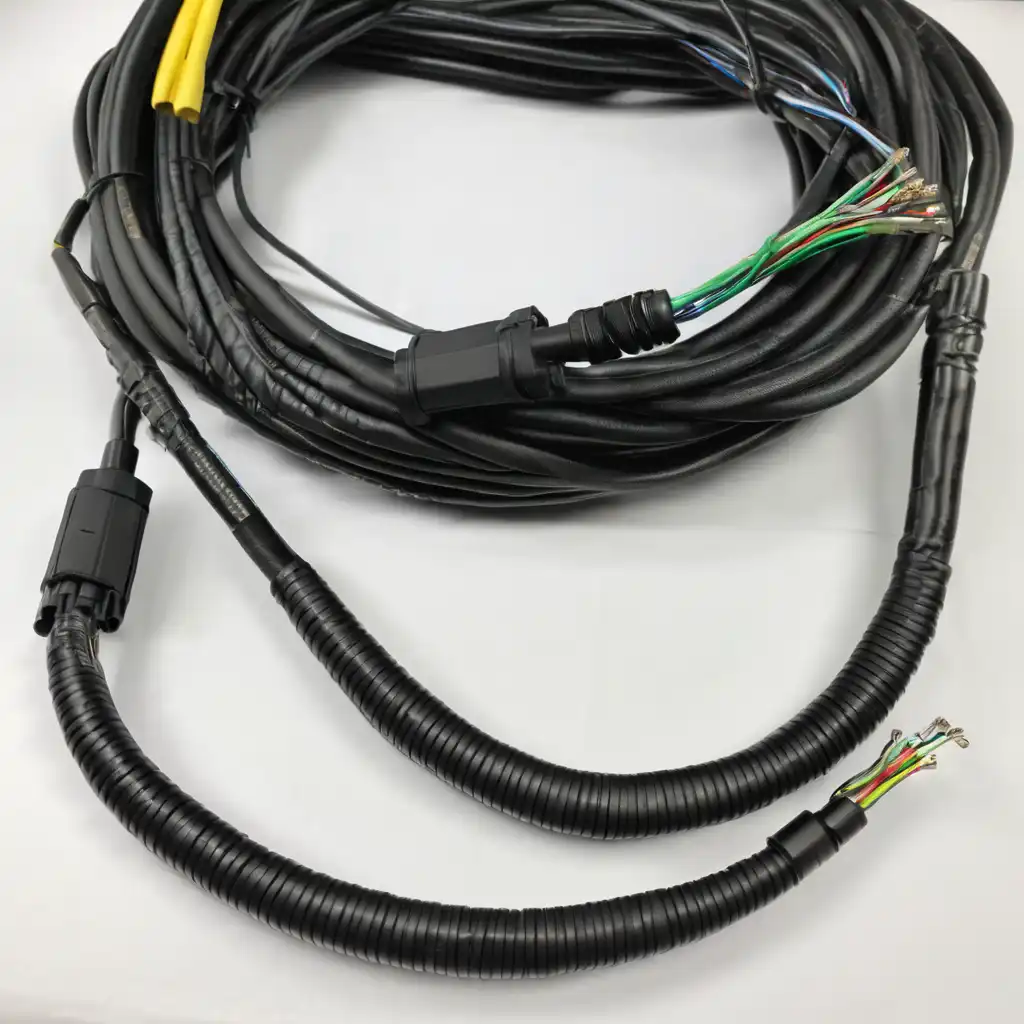
5. Environmental testing:
Wiring harnesses must operate in various environmental conditions. To simulate these conditions, they are subjected to environmental testing involving extreme temperatures, humidity, and vibration exposure. This stress testing ensures that the final product is robust and reliable.
6. Final Quality Audit:
Any wiring harness is subjected to a final quality audit before it leaves the factory. This assessment comprehensively reviews the entire assembly to ensure that each component meets stringent quality requirements. Only after passing this final checkpoint do we approve the wire harness for shipment to the customer.
Beyond these six basic steps, our commitment to quality extends to an ongoing process of continuous improvement. We actively seek feedback from our customers to understand the performance of our wire harnesses and identify areas where we can improve our products and services. This customer-centred approach ensures that we can adapt to our industries’ changing needs and expectations.
In addition, we invest in the professional development of our employees to ensure that they are up-to-date on the latest technologies and techniques. Our team is our greatest asset, and by developing their skills, we uphold a culture of quality that permeates every product we manufacture.
In short, meticulous attention to detail is the cornerstone of our quality control process, from material selection to final review. As a specialized wire harness manufacturer,our fully equipped testing facilities and dedication to excellence ensure that our customers receive only the best,most reliable harnesses on the market.Through these unwavering practices and commitment to continuous improvement,we have not only met but exceeded our customers’ quality expectations,establishing us as a leader in the wire harness manufacturing industry.