Choosing the correct electronic wiring harness is a critical decision that can significantly impact any electrical system’s performance, safety, and reliability. Whether you are designing an automobile, an industrial machine, or a consumer electronic device, an electronic wiring harness’s complexity and critical role require careful selection.As a specialized harness manufacturer, we understand the complexities of selecting the proper harness and are here to guide you through the key factors to consider.
- Application requirements:
The first factor to consider is the application for which the electronic harness will be used. Different applications have different requirements regarding electrical loads, environmental conditions and mechanical stresses. For example, automotive harnesses must withstand extreme temperatures, vibration and chemical exposure. Industrial applications may require harnesses that are resistant to abrasion, while consumer electronics require compact and flexible harnesses.
Understanding these requirements will help you select a harness that meets your project’s specific needs. Our expertise allows us to design and manufacture customized harnesses for various applications, ensuring optimal performance and longevity.
2. Material selection:
The choice of material for the wire and insulating jacket is critical to the durability and functionality of the harness. Conductors are typically made of copper or aluminium, with copper being the preferred choice due to its excellent conductivity and reliability. However, aluminium can be used in applications where weight is critical.
Insulating jackets commonly use materials such as PVC, Teflon, or silicone. Each material has different properties, such as heat resistance, flexibility, and chemical resistance. Our extensive experience in materials science allows us to recommend the best material for your specific application, ensuring a robust and reliable harness.
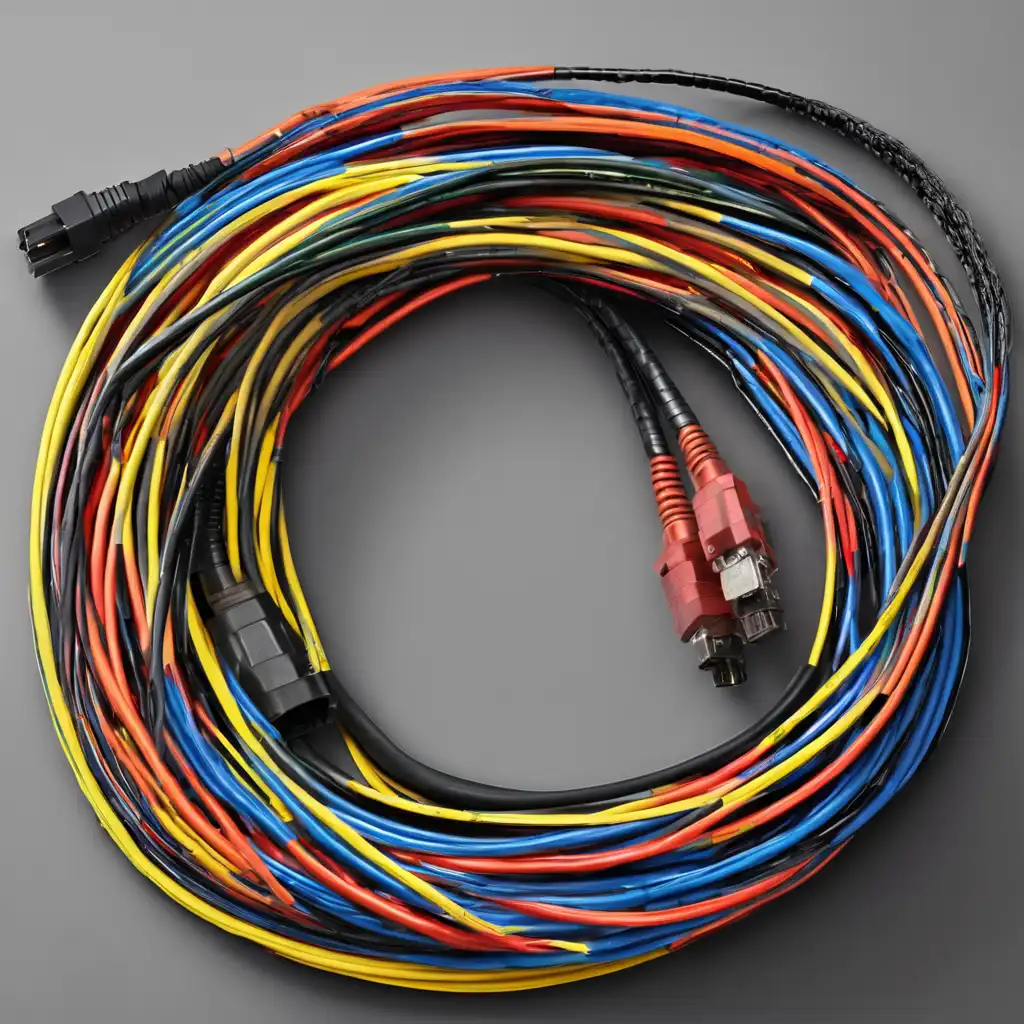
3. Electrical specifications:
Meeting a system’s electrical specifications is critical to the safe and efficient operation of an electronic harness. These specifications include current-carrying capacity, voltage rating, and resistance. It is essential to ensure that the cable can withstand electrical loads without overheating or experiencing significant voltage drops.
We conduct thorough electrical testing and evaluation to ensure that the harnesses we provide meet or exceed the required specifications, giving you peace of mind and ensuring the safety of your application.
4. Compliance and Standards
Compliance with industry standards and regulatory requirements is a non-negotiable aspect of selecting an electronic wire harness. Depending on the application, the harness may have to meet specific certifications and standards, such as ISO, UL, or RoHS approvals. These standards ensure that the harness is safe, reliable and environmentally friendly.
As a reputable wire harness manufacturer, we strictly adhere to all relevant standards and certifications to ensure our products meet the highest quality and safety benchmarks.
5. Design and Configuration
The design and configuration of a wiring harness play a critical role in its installation and function. Consider factors such as wire length, connector type and size, and the overall layout of the harness. A well-designed harness simplifies the installation process and improves system performance by minimizing electrical interference and signal loss.
Our design team works closely with our customers to develop harness configurations that match their system requirements perfectly. We use advanced design tools and techniques to create harnesses that are easy to install, maintain, and troubleshoot.
6. Environmental Factors
Environmental conditions can significantly affect the performance of an electronic wire harness. Factors such as temperature, humidity, chemical exposure and mechanical stress must be considered. Harnesses designed for high-temperature industrial environments differ significantly from harnesses used in consumer electronic devices in controlled indoor environments.
We utilize our extensive knowledge of environmental factors to advise on appropriate harness design and materials. This ensures that the harnesses operate reliably even under the harshest conditions.
7. Cost and budget
While selecting a high-quality harness that meets all technical requirements is essential, cost and budget considerations should not be overlooked. Balancing quality and affordability is critical to ensuring the project’s economic viability. Consider not only the initial cost but also the long-term reliability and maintenance costs.
As a specialized manufacturer, we offer cost-effective solutions without compromising on quality. Our efficient production processes and economies of scale allow us to provide competitive pricing while delivering harnesses that stand the test of time.
Selecting the proper electronic wire harness requires a thorough evaluation of various factors, from application requirements and material selection to electrical specifications and environmental conditions. Ensuring compliance with industry standards and finding the right balance between quality and cost are equally essential steps in the process.
At TESTECK, we pride ourselves on our expertise and commitment to excellence in wire harness manufacturing. By working closely with our customers, we provide customized solutions that meet the highest performance, safety and reliability standards. Let us help you navigate the complexities of selecting the perfect electronic harness for your needs, ensuring your project’s success and long-term sustainability.