When determining the best wire insulation for an electrical application, the comparison between Polytetrafluoroethylene(PTFE)and silicone wire often arises. While both materials are used in high-performance wire and cable applications, they have distinct properties that may make one more suitable for specific circumstances. Is PTFE and Silicone Wire the same?
What is PTFE Wire?
PTFE, also known as Teflon, is a fluoropolymer with remarkable chemical resistance and can perform in high- and low-temperature environments. PTFE-insulated wires are known for their superior dielectric strength, which enables them to resist high-voltage applications without significant degradation. Moreover, PTFE is known for its low friction coefficient, non-stick nature, and non-reactivity to almost all chemicals, making it an excellent insulator in harsh chemical environments.
The longevity of PTFE wire is notable; it can withstand temperatures ranging from -65 °C to +260 °C and, in some unique formulations, up to+300°C. This makes PTFE wire suitable for aerospace, defence, and industrial applications where thermal stability is crucial. Additionally, PTFE insulation is very dense, which provides an extra layer of protection against abrasion and other mechanical stresses.
The Advantages of Silicone Wire
On the other hand, silicone wire is insulated with silicone rubber, a material known for its flexibility, elasticity, and thermal stability. Silicone can remain flexible over a wide temperature range from -55 °C to+180°C. It’s also inherently resistant to UV light, ozone, and many forms of radiation, making it a good choice for outdoor applications.
Silicone’s greatest attribute is its flexibility, which makes it ideal for applications where the wire must be installed in tight spaces or around tight corners. It can handle a lot of bending and twisting without breaking or deforming. Plus, silicone has good dampening properties, which helps reduce vibrations.
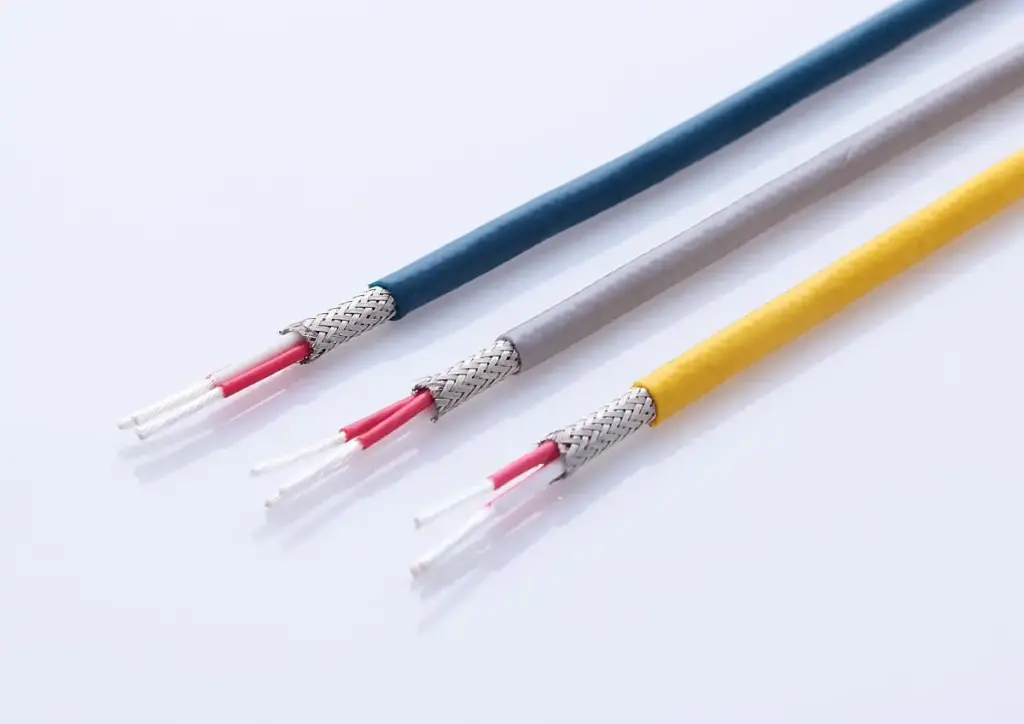
Performance in Extreme Conditions
While PTFE can endure higher temperatures than silicone, silicone’s elastomeric nature is better suited to applications requiring greater flexibility, both materials perform well in extreme conditions, but their distinct physical and chemical properties suit different environments.
For example, in a medical setting where cleanliness and non-reactivity are crucial, PTFE’s PTFE’s biocompatibility can make it the preferred choice. Aerospace applications, which involve high temperatures and require reliable performance, often utilize PTFE because of its comprehensive range of resistant properties and ability to handle rapid temperature changes.
Considerations for Selection
Choosing between PTFE and silicone wire depends on several factors. The specific application’s temperature range, exposure to chemicals, need for flexibility, dielectric strength, and potential exposure to abrasions or mechanical wear all play a part in selecting the appropriate wire insulation. Cost also may be a consideration as PTFE is often more expensive than silicone; however, the investment can be justified by its longevity and robust performance in demanding environments.
As a specialized PTFE and silicone cable manufacturer, we understand that wire performance is critical. Our manufacturing process focuses on creating cables that meet and exceed industry standards. Establishing a solid quality control system ensures that every cable we produce has the resilience and reliability required for high-risk applications.
Our team constantly works on innovations in cable technology and improving material compounds to provide solutions tailored to our customer’s specific needs. With our expertise, we offer cables that meet precise specifications for electrical, mechanical, or thermal properties.
While PTFE and silicone wire insulation serve to protect and insulate electrical conductors, they are not the same. Each material has unique properties and benefits, making it ideal for different applications. As a user, it is essential to understand the environment where the wire will operate to select the most appropriate insulation. Our PTFE wireline is an excellent choice for any application that requires the highest performance, significantly where high temperatures, chemical resistance, and durability cannot be compromised. We are at the forefront of the speciality cable manufacturing industry, committed to providing cables that ensure safety, efficiency and long-term reliability.