Engineers and electricians must select the suitable insulation material for electrical wiring. Two of the most common materials encountered in this decision-making process are PTFE and FEP. While both originated from the same family of fluoropolymers and possess similar properties, critical distinctions between PTFE wire and FEP wire significantly impact their applications and functionality. Here, we will meticulously explore these differences, ensuring you make an informed choice for your needs.
Introduction to PTFE and FEP
Before diving into their differences, it is essential to understand what PTFE and FEP are.PTFE stands for PolyTetraFluoroEthylene, commonly known by its brand name Teflon, trademarked by Chemours(formerly DuPont).PTFE is renowned for its high melting point and non-reactive properties. On the other hand, FEP is shorthand for Fluorinated Ethylene Propylene. While sharing many attributes with PTFE, FEP is noticeably different in some aspects.
PTFE Wire Properties and Usage
PTFE wire boasts outstanding resistance to heat, with a working temperature range from -75 °C to+260°C. It is also highly resistant to chemicals and has one of the lowest coefficients of friction of any solid, which effectively translates to non-stick applications. PTFE’s excellent dielectric properties make it the preferred choice for applications requiring superior electrical insulation, such as military and aerospace technologies.
FEP Wire Properties and Usage
FEP wire, while maintaining a lower heat tolerance than PTFE(operating range between -70 °C to +200 °C), offers some advantages over its counterpart.FEP is more transparent and possesses better gas and vapor permeability properties. Its lower melting point facilitates easier processing and allows for a smoother and more uniform coating, which can be significant in wire insulation applications. Moreover, FEP’s flame resistance and durability make it a favored option for environments where safety and longevity are paramount.
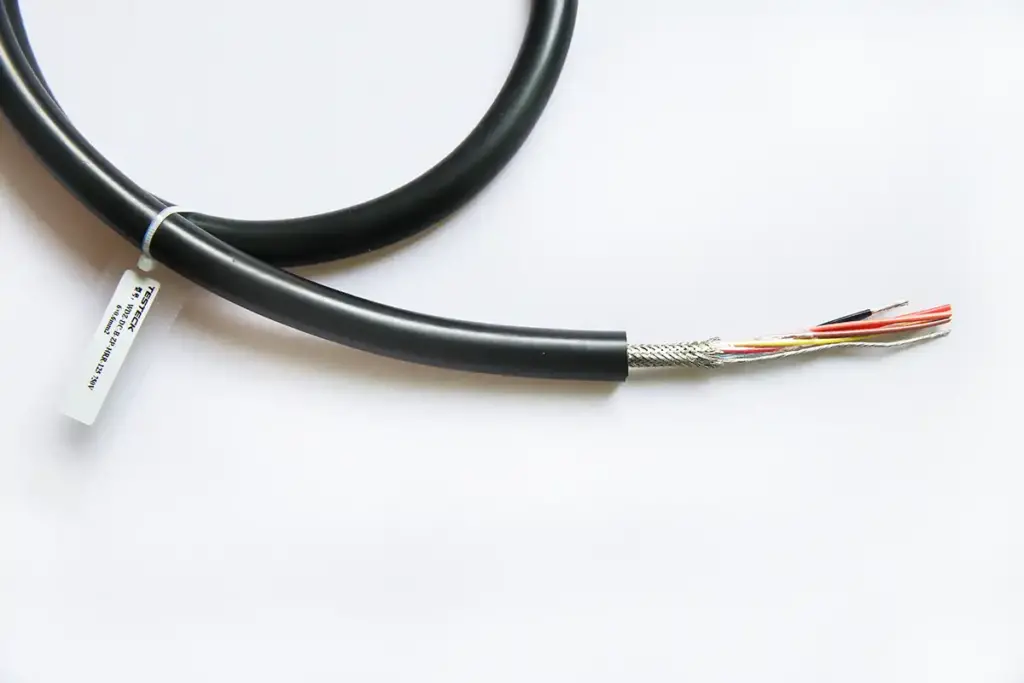
Critical Differences Between PTFE and FEP Wire
The core differences between PTFE and FEP wire can be grouped into the following categories.
Temperature Range: PTFE has a broader temperature range than FEP, which may be a deciding factor for high-temperature applications.
Ease of Processing: FEP is more straightforward to form and manipulate due to its lower melting point, which is beneficial in manufacturing processes.
Dielectric Strength: While FEP and PTFE have excellent dielectric properties, PTFE has a slightly higher dielectric strength.
Mechanical Properties: PTFE is relatively more flexible, while FEP tends to be stiffer, which affects the choice of application for flexibility.
Transparency: FEP is more evident than PTFE, which can be important for specific visual monitoring applications.
Cost Typically: FEP is less expensive than PTFE, which might make FEP more attractive for budget-sensitive projects.
Choosing Between PTFE and FEP Wire
The choice between PTFE and FEP wire depends on your specific requirements.PTFE wire might be the appropriate option for environments involving extreme temperatures or needing the highest level of dielectric strength. Conversely, if you require a material that offers better clarity, slightly better chemical permeation resistance, or a cost-effective solution without significantly compromising on performance, FEP wire could be the suitable selection.
Both PTFE and FEP wires have unique advantages catering to distinctive practical requirements in electrical insulation. Understanding the disparities in their properties is crucial to ensuring that you pick the best option for your project, balancing factors such as temperature stability, electrical insulating qualities,cost-efficiency, and the mechanical demands of your application. By carefully considering these aspects, you can harness the full potential of these exceptional materials and contribute to the efficiency and durability of your electrical wiring systems. You are welcome to contact us for the price of the PTFE cable/FEP wire.